What is the Difference Between Discrete, Process and Batch Manufacturing?
I need to dispel an all-too-common myth.
Not all manufacturing is the same.
That means not all manufacturing software works for every manufacturer.
Business processes, and thus requirements, vary widely according to industry segments such as discrete manufacturing and process, including batch, manufacturing.
Most of the focus in the software world is put on discrete manufacturing, and many software solutions fit that market segment pretty well. However, it has been said that as much as 30% of the manufacturing industry belongs to the process or batch segments – a number large enough that it should not be overlooked.
How Is Process and Batch Manufacturing Different from Discrete Manufacturing?
Let’s start with discrete manufacturing. It’s a large segment, and it well defines what the average person views “manufacturing” to be. Assembly lines, repetitive processes, consistency, quality control. For example, imagine a circuit board manufacturer. Every product should leave the assembly line identical to the last. The same bill of materials for each product, the same components, arranged in the same fashion. If a unit doesn’t measure up, it’s rejected and tossed aside. There are other concepts within discrete, such as engineer-to-order, but they’re variations on the same theme.
Some try to lump process and discrete manufacturing together. However, process is its own animal. While one might talk in terms of batches or even continuous flow products, such as water treatment plants, petroleum refineries, and the like – there’s the element of consistent process.
Within process manufacturing, batch manufacturing is even more unique. And that is the area we choose to focus on.
Batch manufacturing expects to do things differently for each run. It is not simply because they create a variety of products, but because the very nature of their art deals with highly variable factors – varying yields, lot variations in raw materials, variances by production location and equipment, packaging, and more. This means the software system for batch and process manufactures has to be very flexible.
Discrete manufacturing does the process the same way every time. Their software system needs to make sure it is done the same way and not allow for flexibility.
Unique Challenges Not Met by Traditional Manufacturing Software
There are many scenarios unique to process manufacturing that highlight the feature gap in software designed for discrete manufacturing.
Here are a few:Many SKUs, One Formula. Many Formulas, One SKU.
In discrete, the SKU of a final product is usually tied to its bill of materials (BoM). “These are the components that went into the product in your hand,” simple. Such information would change for each product made. However, in batch, you can have several products with different SKUs, but with one formula across them all. For example, we’ll look at beer. One very large batch is produced in a tank. Then it is packaged in kegs, cans, and bottles. Perhaps it’s even put into a serving tank to draw from in a tasting room. On paper, the “products” are different, but in reality, all of the packages are filled from one source with the same formula. Can you imagine the potential for error if the same formula and lot information had to be entered separately for each product?
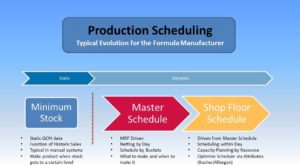
Production scheduling becomes more complex when multiple SKUs are connected to the same formula. Returning to the example of beer, you don’t simply plan to produce so many bottles, so many cans, and so many kegs; rather, you need to schedule the production of one (or multiple) batches of the formula, and divide it accordingly to fulfill the SKU orders. The software needs to be able to handle multiple end items against each batch ticket.
Another challenge in batch is that the same product may have multiple formulas. Locally available ingredients can vary in composition, creating the need for formula adjustments to maintain product consistency. At Sierra Nevada Brewing Company, they face this exact challenge. Having operations in Chico, CA and Mills River, NC, they find a variance in one key ingredient – water. So they must adjust the formula used in each location to ensure that their beer tastes the same regardless of where it was brewed. That’s just one instance; whether producing chemicals or food, ingredients vary by lot, thus requiring constant adjustment. Discrete processes expect the components to be identical in every case; otherwise they are discarded. Thus, standard software solutions often require workarounds or extensive customization to cope with the variable nature of batch manufacturing.
Industry-specific software can assist in making these adjustments, and tracking actual raw material usage. The software can compensate for the lot variance of one ingredient by recommending an increase or decrease of another ingredient. A certain lot of a liquid raw material may have higher water content than normal. Thus, the amount of water added to the formula could be reduced to compensate.
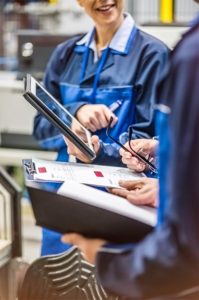
Quality Control
Quality control is an important phase of the process in all segments of the manufacturing industry. In discrete, faulty components or faulty finished products are identified and discarded – a simple “accept” or “reject” decision. In batch, however, samples of the product are evaluated, and if they don’t meet specifications, you don’t simply discard the whole batch; rather, you adjust the mix. Perhaps you add more water, or sugar, or whatever change is necessary to bring it in line with quality and consistency standards. There is more bidirectional communication between quality-control personnel and the production department; that is to say, there’s a tighter link between the two.
Then there’s the separation of quality control processes. Once the batch has passed inspection, it is packaged, which brings another round of quality checks, such as fill level detection, among others. The SKU of the finished product needs to be tied to multiple quality control approvals.
Variable Yields
There are times that you put in 100lbs of raw materials, and the batch yields 90lbs of finished product. The next day, the same materials and the same process yields 85lbs. Another time, 95lbs. In the world of batch manufacturing, 1 + 1 does not always equal 2. Sometimes it equals 3, other times 1 and a half. Your ERP solution needs to be able to account for these variances because they affect production scheduling and affect stock levels of your raw materials, as well as the resulting costs incurred for each batch.
In a discrete scenario, you expect a certain percentage of loss, and it’s pretty consistent. You put in 100 units, and you get 95 out, resulting in a 5% loss. However, when dealing with different ingredients, the loss calculations become more complex. Many products have both liquid and solid ingredients. If, for example, part of the process involves evaporation, any liquid components will have more loss than solid ones.
This becomes especially challenging when scaling formulas. In made-to-order scenarios, the batch size fluctuates depending on the customer’s request. It’s not simple multiplication or division; these loss factors have to be taken into account.
Therefore, the concept of back-flushing is typically not used in batch manufacturing. Instead, actual input is compared with actual output, taking into account the varying yields. This approach allows you to accurately calculate costs, schedule production, and plan raw material usage.
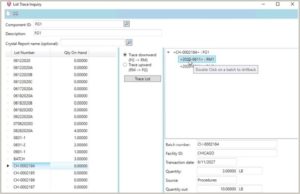
Lot Traceability
Long runs and sub-batches present difficulties in lot traceability. A bakery might run all day, producing multiple batches of dough from the same stock of ingredients throughout the day. Through the production line, the dough is divided, baked, and packaged. The ingredients are the same, the formula is the same, but there are multiple runs involved throughout the course of the day. They’re all part of one lot, but some companies need to divide the product into sub-batches and identify them accordingly.
The need for this functionality becomes especially acute when dealing with FDA lot traceability requirements (21 CFR Part 11). Every ingredient of the final product, and everything that touches the product during the process, must be traceable. There might be raw material intermediate, such as a partial mix in a holding tank awaiting use in the next stage of production, as well as the finished goods and packaging that would need to be tracked. And there are other phases, such as reworked product, byproducts, etc. The ERP software needs to be flexible enough to meet all these needs.
Regulatory Compliance
Regulatory compliance takes many forms in batch manufacturing. In the food sector, there’s the famous Nutrition Facts label. Those figures – quantities and percentages – are provided by you, the manufacturer, and calculated based on your formula (the ingredients you use.) Your data may come in part from your suppliers, who provide you with the nutritional information for the raw material they’re selling you. You determine the serving size and then calculate the figures to produce a final label.
Chemical manufacturers face another set of compliance issues. Bills of Lading (BoL) must classify, using standard hazardous material codes, the chemical nature of the product. In case of spills or other accidents, this enables emergency personnel to properly respond (bringing in the fire department, a hazmat team, or the like.)
Some of that reporting also comes in the form of the GHS SDS. Years ago the United States had its own standard, the MSDS, but later the United Nations became involved to create an international standard, with placards and pictograms, along with standards on how to disclose necessary technical information. Information about the product must be compiled and disclosed according to that standard – and it ultimately comes from the formula, the ingredients that go into the batch. There are more industry-specific requirements, such as SARA 312 and 313, which track the storage and use of hazardous materials. Software assistance greatly automates the process and ensures compliance.
How to Meet the Needs of Batch Manufacturers
Many choose to start with a general manufacturing solution and have their VAR partner customize it until it meets their needs. This can become very involved and costly – and complicate the upgrade process in the future when those customizations don’t work with the latest version of the platform.
There is a better way.
Selecting an ERP solution with batch manufacturing support out-of-the-box saves a great deal of time and money in the implementation stage and provides a clear upgrade path for the future. Being developed specifically for your industry, the software continues to provide new functionality that further enhances your operations with each new version.
Vicinity Software offers such solutions for the chemical, food, and brewing segments of the manufacturing industry. Contact us today to learn how we bridge the gap for batch manufacturing.
By Randy Smith, CEO and Co-founder, Vicinity Software
If you are not a customer of Vicinity Software, contact us today for a demo and to learn more about how we can support your business. Contact Us Today!